Produktionspalette
- stromisolierende Schichten
- stromleitende Schichten
- wärmedämmende Schichten
- wärmeleitende Schichten
- korrosionsverhindernde Schichten
- verschleißfeste Schichten
- Hartchrom Ersatz Schichten
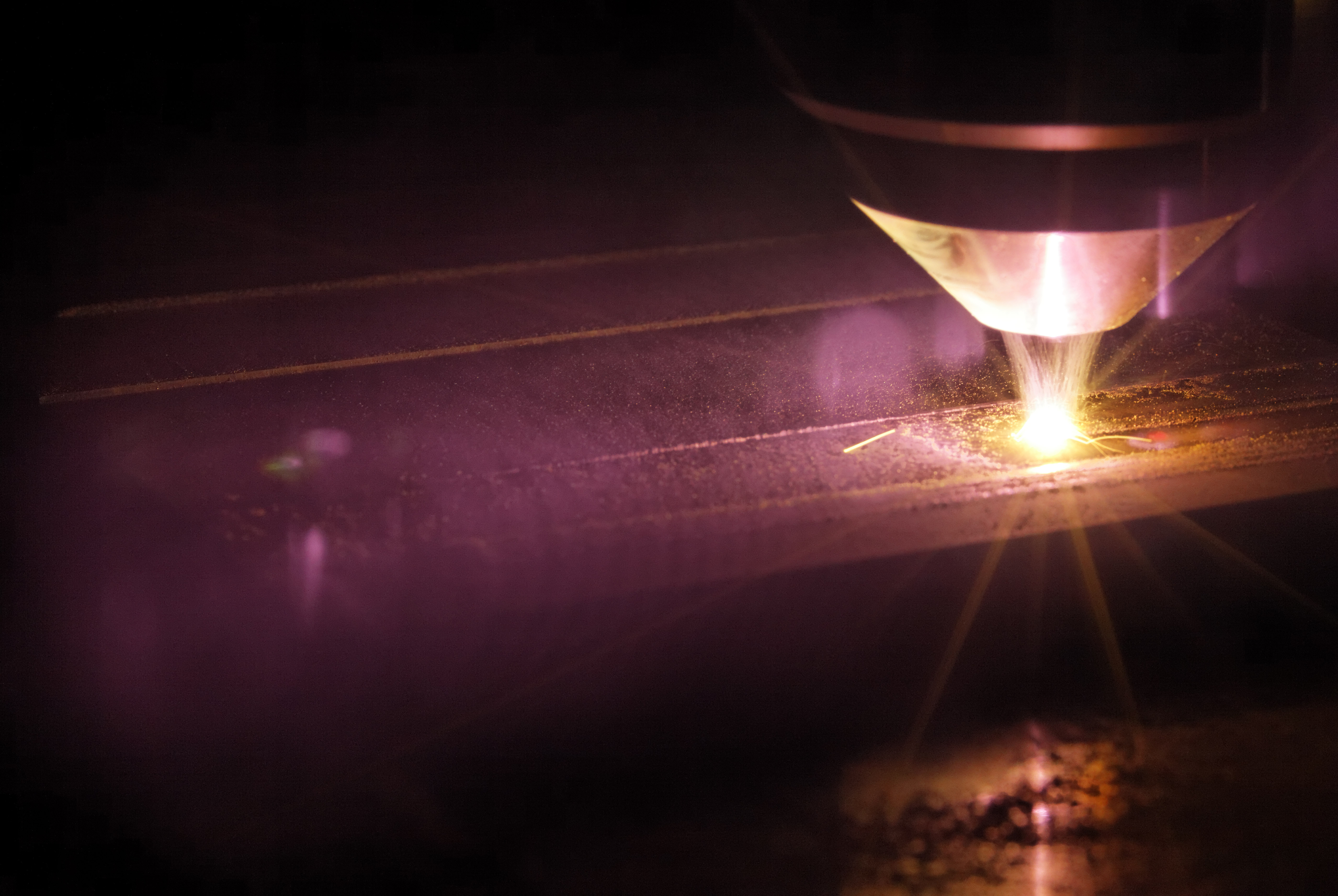
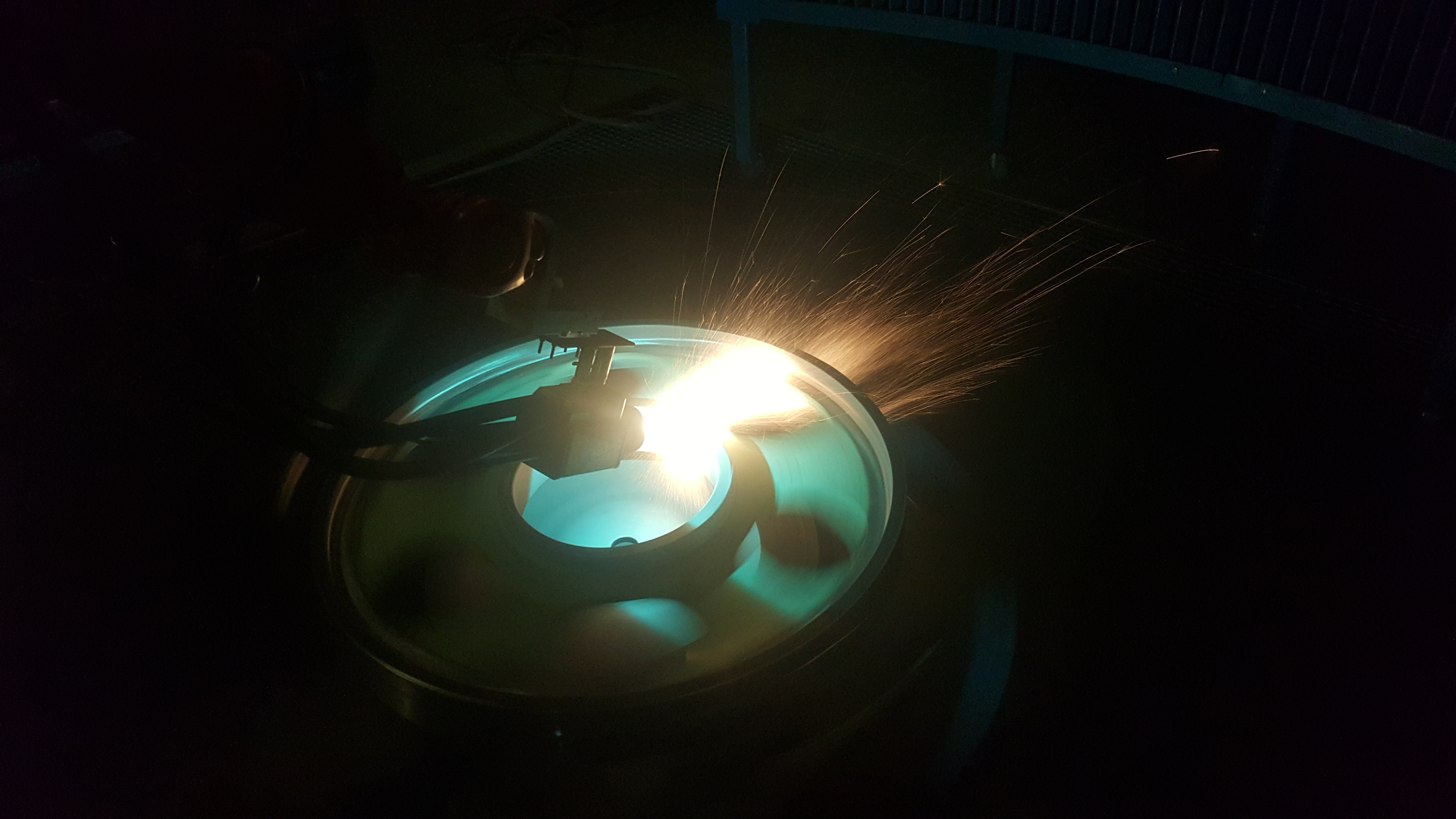
Anwendungsbeispiele
- Wiederherstellung einer Originalabmessung (Reparatur & Ausschussrettung)
- Verbesserung des Verschleiß- und Korrosionsschutzes
- Verbesserung der Gleitfähigkeit (Selbstschmierung)
- raue, widerstandsfähige Oberflächen (Mitnehmer, Greifer, Reibbeläge)
- Gewichtseinsparung (leichter Grundwerkstoff mit hoher Oberflächenqualität)
- Kostenreduktion (billigerer Grundwerkstoff => hochwertigere Schicht)
- stromisolierende Lagerringe (verhindern Stromfluss durch das Lager)
- elektrische Schalter für verbesserten Stromfluss (Verkupfern / Versilbern)
Hartchrom Ersatz
Aus Bewusstsein für die Gesundheit und den Umweltschutz gibt es massive Restriktionen bei der Verwendung von hexavalentem Chrom. Als Alternativen zum Hartverchromen haben sich unter anderem das Thermische Spritzen und HVOF Verfahren bewiesen. Vor allem HVOF Schichten bieten technologische Vorteile. Dazu gehört, dass HVOF Schichten hohe Druckeigenspannungen aufweisen können, die sich positiv auf die Festigkeit der beschichteten Bauteile unter dynamischer Belastung auswirken. HVOF Schichten auf der Basis von Wolframcarbid haben für viele Arten tribologischer Belastung eine wesentlich höhere Verschleißbeständigkeit. Sie weisen sich ebenfalls durch eine kürzere Produktionszeit aus und es besteht keine Gefahr der Wasserstoffversprödung. Aufgrund dieser Attribute konnten sich HVOF Schichten gegen Hartchromschichten durchsetzen und werden in verschiedenen Bereichen eingesetzt wie zum Beispiel Flugzeugfahrwerksteile, Hydraulikzylinder, Walzen für die Formgebung und ähnliches.
Die Alternativen zu Hartchromschichten bieten neben umweltschutztechnischen Gründen weitere technische Vorteile:
- Verbessertes Abnutzungsverhalten, besonders bei dickeren Schichtstärken. Es entsteht bei gleichzeitig gutem Korrosionsverhalten ein geringerer Aufwand für die Reparatur und Wartung.
- optimierter Eigenspannungszustand
- stark verbessertes Ermüdungsverhalten
- minimierte Anfälligkeit für Lochfraßkorrosion beim Einsatz in feuchter und korrosiver Umgebung
- minimierte Anfälligkeit für Mikrorisse auf Grund von höherer Duktilität
- Geringere Lebenszyklus-Kosten: die höhere Langzeit-Performance führt zu deutlichen niedrigeren Instandhaltungskosten. Durch HVOF-Verfahren werden Teile auch schneller bearbeitet, was zu einer kürzeren Ausfallzeit der Bauteile und Komponenten führt.
- breiteres Spektrum von Substrat-Werkstoffen/Pulvern möglich
- keine Begrenzung durch Bauteilmaße
- einfachere Reparaturmöglichkeit und problemlose partielle Beschichtung von Neuteilen
- zeitsparendes Beschichten von Teilen mittlerer Größe und Großbauteilen
- weniger Prozess-Schritte
- weniger Abfall und geringere Kosten für die Müllentsorgung