Production range
- current insulating coatings
- electrically conductive coatings
- heat-insulating coatings
- thermally conductive coatings
- corrosion preventing coatings
- wear-resistant coatings
- Hard chrome replacement coatings
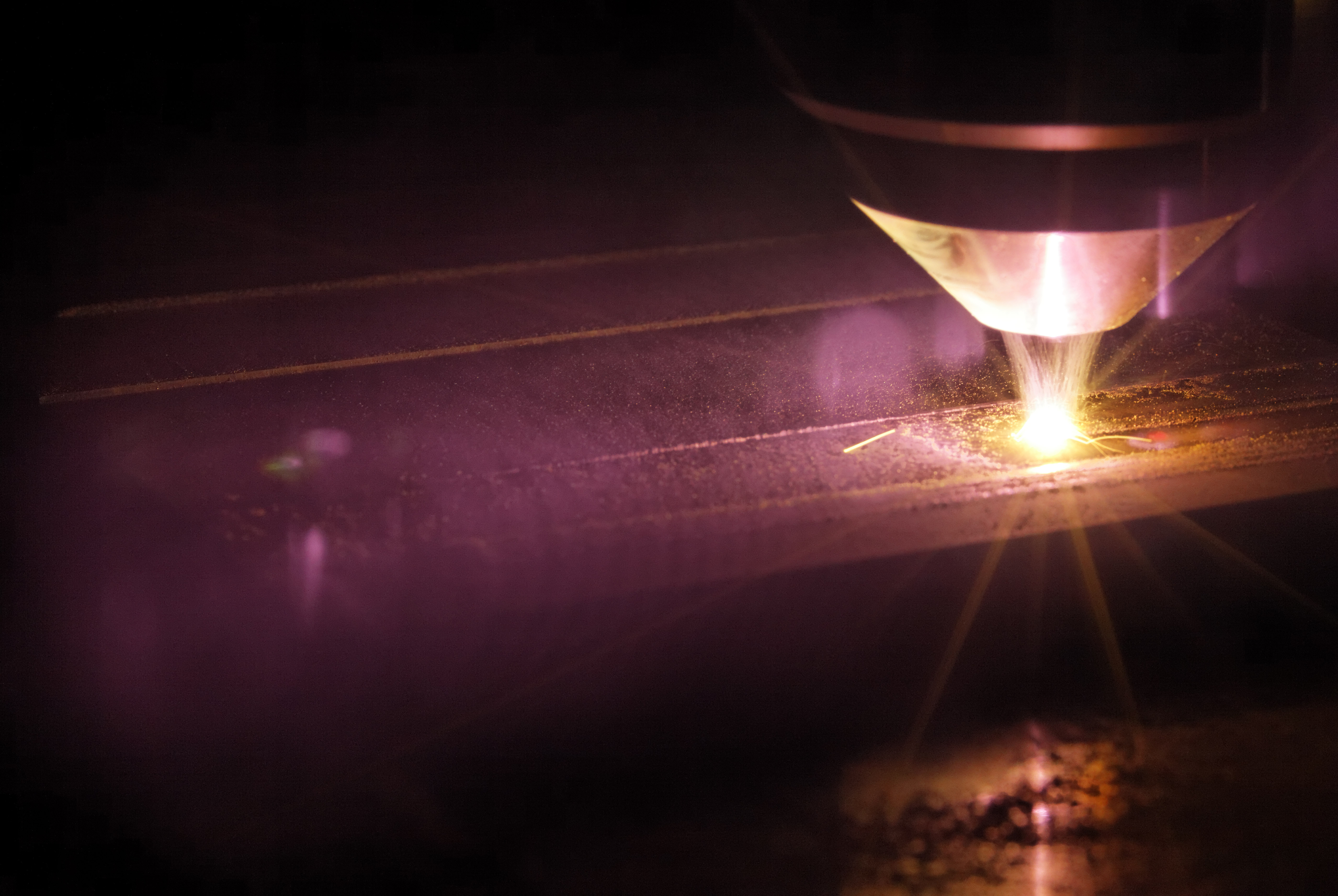
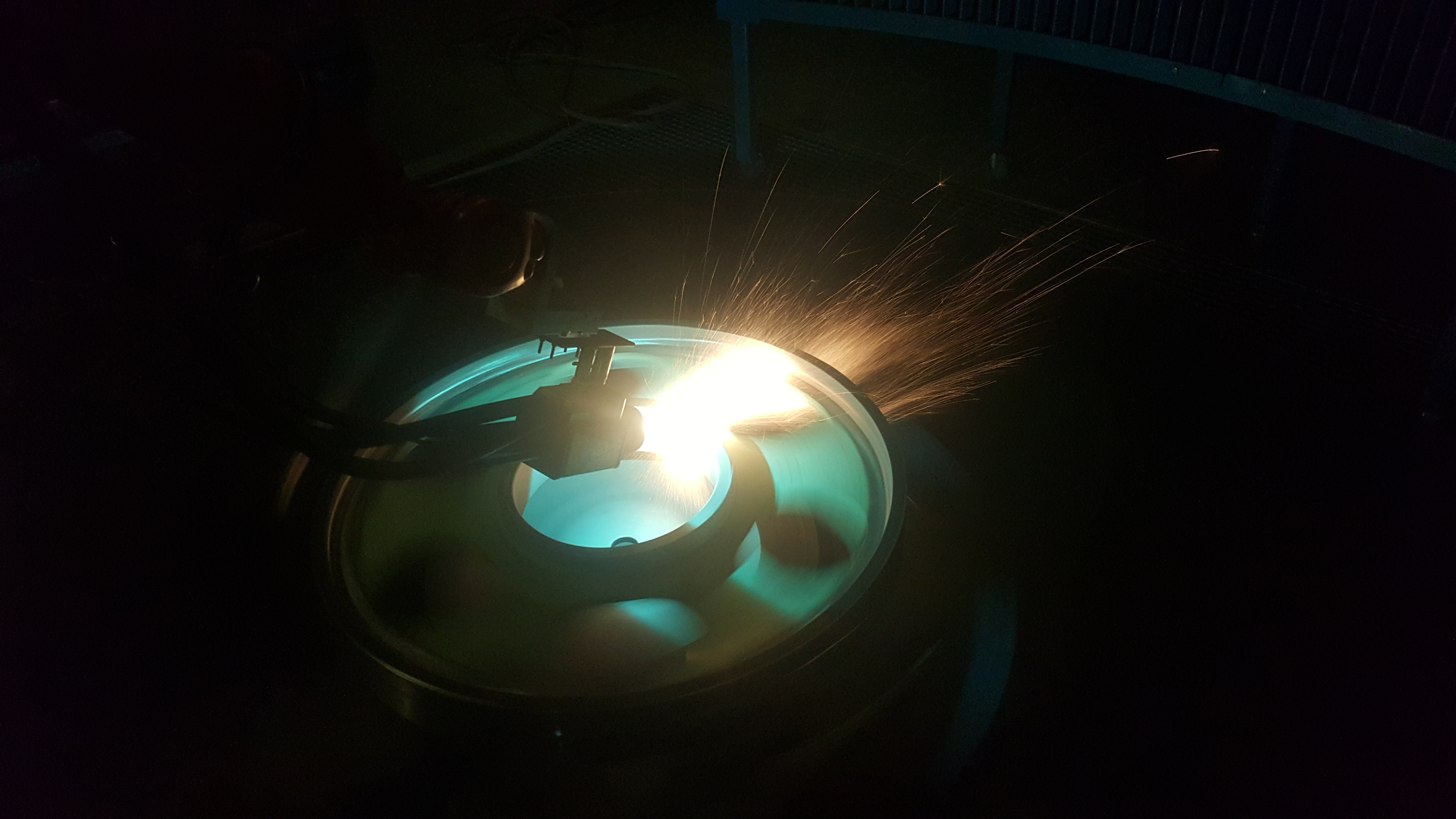
Applications
- Restoration of an original dimension (repair & scrap rescue)
- Improvement of wear and corrosion protection
- Improvement of lubricity (self-lubrication)
- Rough, resistant surfaces (drivers, grippers, friction linings)
- Weight saving (light base material with high quality surface)
- Cost reduction (cheaper base material => higher quality layer)
- Electrical current-insulating bearing rings (prevent current flow through the bearing)
- Electric switches for improved current flow (copperplating / silvering)
Hard chrome replacement
Being aware of health and environmental issues, there are massive restrictions on the use of hexavalent chromium. Thermal spraying and HVOF processes have proved to be alternatives to hard chrome plating. Especially HVOF coatings offer technological advantages. This implies that HVOF layers can have high residual compressive stresses which positively affect the strength of the coated components under dynamic loading. Tungsten carbide based HVOF coatings have much higher wear resistance for many tribological load types. They are also characterized by a shorter production time and there is no risk of hydrogen embrittlement. Due to these attributes, HVOF coatings were able to assert themselves against hard chrome coatings and are used in various areas, such as aircraft landing gear components, hydraulic cylinders, forming rolls and the like.
The alternatives to hard chrome layers offer other technical advantages in addition to environmental protection reasons:
- Improved wear behavior, especially for thicker layers. At the same time good corrosion behavior results in less effort for repair and maintenance.
- optimized residual stress state
- greatly improved fatigue behavior
- minimized susceptibility to pitting corrosion when used in humid and corrosive environments
- minimized susceptibility to microcracks due to higher ductility
- Lower lifecycle costs: the higher long-term performance leads to significantly lower maintenance costs. With HVOF processes, parts are also processed faster, resulting in shorter downtime of components and components.
- wider range of substrate materials/powders possible
- no limitation due to component dimensions
- easier repair and problem-free partial coating of new parts
- Time-saving coating of parts of medium size and large components
- less process steps
- less waste and lower waste disposal costs